Do napisania dzisiejszego postu natchnął mnie nie tylko webinar, swoją drogą bardzo interesujący, ale również rozmowy i obserwacje tego jak 5S jest wdrożone i jak funkcjonuje w różnych organizacjach czy też poszczególnych obszarach.
Trzeba otwarcie przyznać, że różnie z tym bywa. Różne jest rozumienie samej techniki jak również potrzeb i sensu jej wdrażania. Nie mam zamiaru oczywiście demonizować i twierdzić, że 5S nie funkcjonuje z takiego czy innego powodu. Bardziej będę się starał wskazać czym 5S właściwie jest, choć to może wydawać się na pierwszy rzut oka bardzo trywialne, ale też co zrobić aby uniknąć podstawowych błędów przy jego wdrażaniu.
5S podstawy
Oczywiście nie mogę pominąć kwestii teoretycznej, której oczywiście jest na pęczki w internecie i nie tylko, ale pomijając ten element trudniejszym zadaniem będzie wyjaśnić jakich błędów powinniśmy się wystrzegać.
Jak spora część technik i narzędzi wykorzystywanych przy metodologii szczupłego zarządzania, tak i 5S swoje korzenie wywodzi z Japonii. Podstawowym założeniem 5S jest uporządkowanie oraz zorganizowanie miejsca pracy w sposób, który przyczyni się do tego, że nasza praca będzie wykonywana w sposób efektywny i co za tym idzie również bezpieczny.
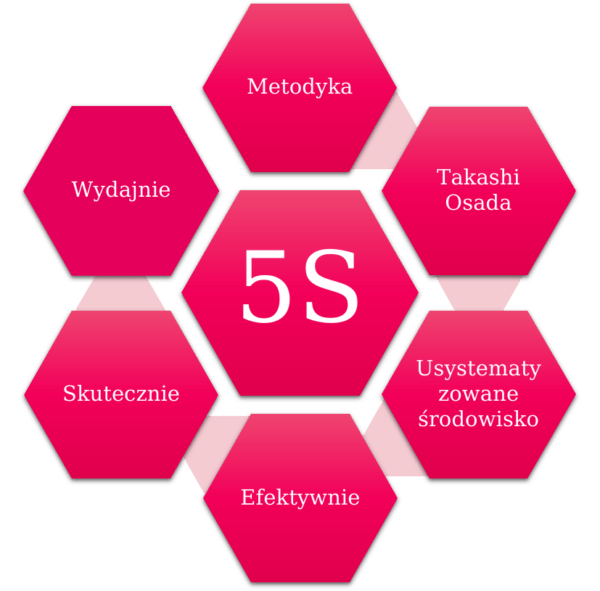
5S krok po kroku
Co zatem kryje się za tym krótkim zwrtotem, przedstawia poniższa grafika, ja natomiast skupię się na tym jak przejść poprzez kolejne etapy, krok po kroku, jakich błedów się wystrzegać aby 5S nie stało się zmorą dla pracowników, a wręcz przeciwnie, zachęciło ich do czynnego uczestnictwa w programie wdrażania i promowania kultury 5S.
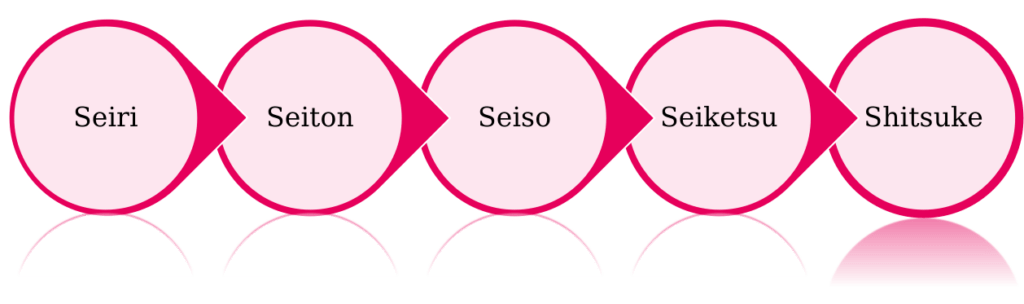
Seiri (ang. sort) polega na sortowaniu i oddzieleniu elementów, które na danym kroku procesu nie są używane lub używane są sporadycznie.
Seiton (ang. set in order) czyli nic innego jak systematyzowanie obszaru, tj. wyznaczenie i przygotowanie miejsc dla wszystkich przedmiotów.
Seiso (ang. shine) sprzątanie polegające na poukładaniu wszystkich elementów uczestniczących w procesie na odpowiednio przygotowanych wcześniej do tego miejscach.
Seiketsu (ang. standarise) udokumentowanie poprzednich trzech kroków w postaci standardów dając wskazówki jak dane miejsce pracy powinno wyglądać.
Shitsuke (ang. sustain) to najtrudniejszy ze wszystkich kroków, zarówno pod kątem wprowadzenia, utrzymania i rozwoju. Samoyscyplina wymaga bowiem zaangażowania pracowników na wszystkich szczeblach organizacji.
Główne przyczyny porażki
Jak każde z rozwiązań wdrażanych w organizcjach, tak i 5S wymaga planowania. Bez tego etapu tak naprawdę, żaden z prowadzonych przez nas projektów, nawet wdrożenia 5S, niezależnie czy będzie to na obszarze produkcji, w biurze czy magazynie nie zakończy sie sukcesem w chwili gdy bedziemy podchodzić do tematu chaotycznie i bez merytorycznego planu.
Poniżej, przedstawiam po skrócie główne błędy stanowiące przyczyny niepowodzeń.
5S w pierwszej kolejności
Tak…i to jest jeden z poważniejszych problemów z jakimi spotykałem się najczęściej. W wielu organizacjach. 5S wdrażane było jako pierwsza lub jedna z pierwszych technik, już na samym początku przygody organizacji z Lean Management.
Pewnie wiele osób się ze mną w tym momencie nie zgodzi, a może będę miał na tyle szczęścia, że liczba głosów za i przeciw się zrównoważy. Tak czy inaczej osobiście uważam, że nie jest to od czego organizacja myśląca o kulturze Lean powinna zaczynać.
Wiem, że wprowadzanie 5S już na samym początku jest kuszące, ponieważ, w dość szybkim czasie pozwala osiągać namacalne i widoczne efekty. Mamy bowiem już od ręki schludne stanowiska, więc po co nam więcej? Efekt osiągnięty, plan zrealizowany, można ogłosić sukces.
I tu pojawia się pierwszy, dość istotny problem. Jeśli zechcemy wdrażać kolejne rozwiązania typu SMED, TPM itd, nasze efekty i wysiłki, jeśli nawet wdrożenia dokonaliśmy zgodnie ze sztuką legną w gruzach, a wszystko to czego dokonaliśmy w międzyczasie, przestanie tak właściwie mieć jakiekolwiek znaczenie.
Dodatkowo problemowi temu towarzyszy inna przypadłość, a mianowicie wdrożenie wszystkich 5 elementów na raz bez zachowania zasad podejścia systemowego do wdrażania jakichkolwiek rozwiązań.
Czego unikać: nie skupiaj się na wdrażaniu 5S na początku wprowadzaniu rozwiązań sczupłego zarzadzania, pamiętając przy tym, że nie jest to tylko i wyłącznie narzędzie mające na celu sprzątanie.
O czym pamiętać: określ cel i zaplanuj systemowe działanie, które będzie spójne z działaniami poprawiającymi efektywność funkcjonowania procesów.
Brak zaangażowania odpowiednich zasobów
Jeden z tych błędów, z którymi można spotkać się najczęściej. W wielu bowiem organizacjach, za wdrożenie 5S jak i pozostałych narzędzi szczupłego zarządzania zajmują się dedykowani do tego pracownicy, tacy jak specjaliści czy kierownicy Lean / Ciągłego doskonalenia. Są to osoby, od których oczekuje się efektów na poprawę funkcjonowania procesów i z których są rozliczane.
Tym samym pojawia się najczęściej problem z brakiem zaangażowania, najczęściej wśród kierownictwa niższego i wyższego szczebla, co w efekcie doprowadza do stanu, w którym, dochodzi do sytuacji gdzie techniki takie jak 5S wdrażane są jednoosobowo bez wsparcia zarówno osób kierujących odpowiednimi obszarami jak i całą organizacją.
W związku z tym, istotne jest by inicjatywa wypływała z samej góry od najwyższego kierownictwa, zgodnie z zasadą Hoshin Kanri, a więc określenia celów strategicznych, a następnie propagowania celów na niższe poziomy. Tym samym, kwestie związane z wdrożeniem 5S czy innych technik i narzedzi szczupłego zarządzania były wspierane przez dostarczenie odpowiednich zasobów na każdym poziomie.
Czego unikać: wdrażania rozwiązań jednoosobowo. Nie szukaj i nie przygotowuj planu bez konsultacji z właścicielami procesu, a przede wszystkim bez udziału pracowników.
O czym pamiętać: jak każde z rozwiązań sczupłego zarządzania, tak i 5S jest techniką, która wymaga zaangażowania i czynnego udziału wszystkich pracowników organizacji na każdym poziomie. Szczególnie ważne jest zaangażowanie i gromadzenie informacji od pracowników na stanowiskach pracy gdzie technika jest wdrażana. Dobrą praktyką jest również wdrożenie eventów mających na celu propagowanie 5S wśród pracowników.
Wszystko zaczyna się i kończy na audycie
Oczywiście samodyscyplina jest elementem 5S. Oczywiście wymaga to weryfikacji i monitorowania statusu wdrożenia oraz utrzymania wszystkich elementów, jednakże nie jest to krok, od którego wdrażanie 5S powinno się rozpoczynać.
Dodatkowo, nawet jeśli 5S zostanie wdrożone zgodnie z zasadami, utrzymanie go przy życiu będzie wymagało trzech podstawowych narzędzi;
- promowanie kultury 5S
- komunikacja celów i wyników
- szkolenie pracowników
Audyt będzie stanowił integralny element tego procesu, ale nie należy stawiać go ponad wszystkim. Ułatwić to może równiesz zmiana nastawienia, a mianowicie przekształcenie świadomości pracowników, że audyt nie jest złem koniecznym, na który pracownicy powinni reagować strachem lub co gorsza irytacją. Audyt / przegląd 5S ma przede wszystkim słuzyć do oceny stanu obecnego i poszukania wspólnie potencjału do rozwoju. Nie jest przecież powiedziane, że pracownik nie przestrzega opracowanych standardów, o ile te w ogóle istnieją, bo jest oportunistą.
A może standard nie jest opracowany w sposób właściwy? Czy pracownik uczestniczył w procesie kształtowanie techniki na swoim miejscu pracy? Czy przeprowadzone były odpowiednie szkolenia?
Czego unikać: prowadzenia audytów w przekonaniu, że jest to główny element samodyscypliny. Dodatkowo audyty nie są narzędziem do wskazywania niezgodności, a do przedstawienia obszarów do doskonalenia dlatego powinny służyć jako wsparcie a nie narzędzie do egzekwowania.
O czym pamiętać: o zaangażowaniu pracowników i stworzeniu systemu, w którym pracownicy będą sami kontrolowali status wdrożenia i utrzymania 5S, które powinno stać się integralną częścią systemu. Warto również wprowadzić Gemba Walks oraz wskaźniki, dzięki którym będziesz mógł stale monitorować postępy.
Safety nie jest 6 elementem
W wielu przypadkach, organizacje decydując się na wdrożenie 5S, a swoją decyzję motywują zapewnieniem bezpieczeństwa. Jest to jak najbardziej słuszne podejście. Porządkując procesy, jak najbardziej przyczyniamy się nie tylko do poprawy efektywności procesów ale również bezpieczeńtswa na stanowiskach pracy, w szczególności jeśli mówimy o procesach wytwórczych, gdzie ryzyko spowodowania uszczerbku na zdrowiu pracowników.
Największym problemem jest jednak przeświadczenie, że bezpieczeństwo (ang. safety) stało się integralną częścią 5S, a właściwie ewoluowało już do 6S. Pęd ku zwiększeniu bezpieczeństwa pracy, prowadzi często do tego, że wszystkie pozostałe 5 kroków wprowadzane jest na raz. Część etapów jest pomijana lub nie jest przeprowadzona w sposób zgodny z założeniami techniki 5S.
Czego unikać: kierowania się przekonaniem, że głównym celem jest zapewnienie bezpieczeństwa jako kolejnego kroku w technice tworząc tym samym nową technikę w postaci 6S.
O czym pamiętać: bezpieczeńtwo nie jest częścią nowego systemu. Jest to skutkek, który bardzo porządanym obok takich elementów jak efektywność, skuteczność i wydajność procesów.
A gdzie standardy?
No właśnie…jest to niestety bolączka, która nie tyczy się jedynie 5S. Wdrażając rozwiązania Lean, a wszczególności 5S standaryzacja jest często pomijana. Dzieje się tak, głównie ze wzglądu na fakt, iż po wdrożeniu pierwszych trzech kroków, efekty są widoczne na tyle, że krok czwarty a więc właśnie standaryzacja jest pomijana.
Mamy bowiem odseparowane narzędzia, wyznaczone miejsca na ich składowanie w postaci tablicy cieni czy też szafek, wszystko jest na swoich miejscach, więc pojawia się przeświadczenie, że wszystko już działa. Problem pojawia się jednak, kiedy zaczynamy egzekwować od pracowników tego co wypracowaliśmy i…okazuje się, że nie ma standardów lub są one niedopasowane do rzeczywistości.
Czego unikać: przede wszystkim sytuacji, w których kluczowym jest pilnowanie porządku na pulpicie komputera lub projektowanie nieprzemyślanych rozwiązań. Takie podejście prowadziło do oporu pracowników przed wdrożeniem i utrzymaniem systemu.
O czym pamiętać: opracowanie i wdrożenie 5S jak również przygotowanie standardów powinno odbywać się przy zachowaniu zdrowego rozsądku oraz dopasowane do obszaru, w którym technika jest wdrażana.
Plan wdrożenia 5S
Wskazane powyżej błędy są najpoważniejsze i stanowią najczęstszą przyczynę problemów towarzyszących przy wdrażaniu 5S. Jak można zauważyć brak skutecznego planowania może zniweczyć skutecznie nasze wysiłki. Dlatego też wdrażając choćby 5S warto sięgnąć po narzędzie jakim jest cykl PDCA, opisywany przeze mnie niedawno.
W skrócie plan wdrożenia przedstawia poniższa grafika.

Jako uzupełnienie, załączam krótki film przedstawiający wdrożenie 5S w 11 punktach, opublikowany przez kanał LeanVlog, a który w sposób zwięzły przedstawia dobre praktyki, które warto zastosować.
Podsumowanie
Dzisiejszego bloga podsumuję krótkim zdaniem.
Nie skupiaj się tylko na sprzątaniu, ale podejdź do procesu systemowo, szcegółowo planując, komunikując i propagując rozwiązania 5S.
A tych z Was, którzy są zainteresowani poszerzeniem swojej wiedzy zapraszam na szkolenie przygotowane przez Lean Management Consulting Group.