W poprzednim wpisie starałem się w jak najlepszy sposób przedstawić, jak prowadzić analizę przyczyn źródłowych. Dziś postanowiłem zagłębić się w temat jeszcze bardziej i przeanalizować oraz pokazać jak wykorzystać w tym celu narzędzie jakim jest 5 Why?. Narzędzie, które jest swoistym kluczem do otwarcia drzwi, za którymi kryją się odpowiedzi na nurtujące pytania oraz przyczyny problemów, z którymi przychodzi nam się borykać w codziennej pracy z procesami.
Dlaczego 5 Why?
5 Why?, lub jak kto woli 5x Dlaczego? to technika wypracowana przez jednego z pionierów zarządzania jakością. Taiichi Ohno, bo o nim mowa, zasłynął nie tylko ze stworzenia Toyota Production System, w którym króluje podejście Just-in-Time. Miał również swój niepodważalny wkład w rozwój Lean Management w USA.
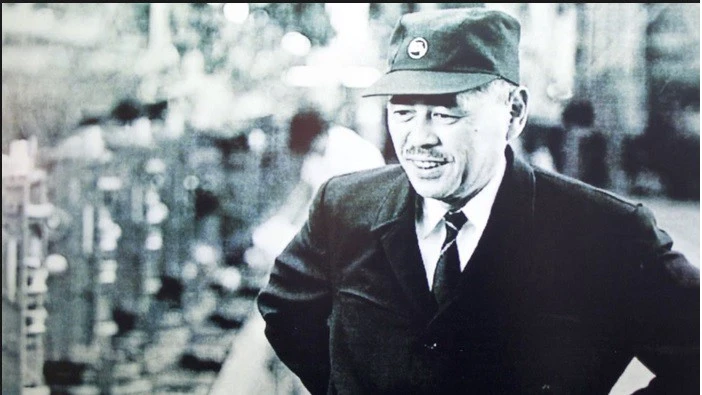
Ale obok tych wielkich dokonań, Taiichi Ohno zasłynął również z opracowania i wdrożenia techniki 5 Why?, która do dnia dzisiejszego, tak samo jak zasady Lean Management i zarządzania jakością, funkcjonują z powodzeniem, a wiele firm chętnie po nie sięga i korzysta z nich w niezmienionej formie do dnia dzisiejszego.
No właśnie! Ale dlaczego właściwie stosować narzędzie 5x Dlaczego?
Odpowiedź jest dość oczywista. 5 Why? to bardzo uniwersalne narzędzie, które pozwala na wyjście z utartych schematów, innymi słowy mówiąc pozwala spojrzeć poza utarte schematy postępowania. Czyli nic innego jak poprowadzić zespół analizujący problem w myśl zasady out of the box thinking.
Te proste pytania potrafią często otworzyć oczy na kwestie, które są nieoczywiste lub trudne do zidentyfikowania jako właściwe przyczyny problemu.
Jak korzystać z 5x Dlaczego?
To jest bardzo dobrze postawione pytanie. Jak korzystać z 5 Why?, żeby dojść do sedna problemu i nie utknąć w nicości ze źle zdefiniowaną przyczyną.
Jak pisałem już przy okazji zagadnień rozwiązywania problemu czy analizy przyczyn źródłowych, ważne jest by zrozumieć istotę problemu. Jeśli wiemy co jest problemem i jaki ma on wpływ na funkcjonowanie naszych procesów, wówczas łatwiej będzie nam dojść do przyczyny źródłowej jego występowania.
Zanim przejdę do omawiania kwestii techniczych korzystania z 5 Why?, to nadmienię, że potencjalna przyczyna powstawania problemu nie zawsze będzie tą jedyną i właściwą, którą można uznać za źródło naszych niepowodzeń. Zauważył to też sam Taiichi Ohno, dlatego zgodnie z ludzką naturą zaczął drążyć dalej zadająć to proste pytanie Dlaczego?
Dlaczego zatrzymał się na 5 a nie 10 czy 3 pytaniach? Cóż nie mam na to jednoznacznej odpowiedzi, ale uznaje się, że pięć pytań oraz udzielonych na nie odpowiedzi jest wystarczające by dojść do sedna powstania problemu a więc do przyczyny źródłowej. Oczywiście nie jest to warunek konieczny i nie ogranicza nas on w tym by koniecznie dążyć do zadania 5 pytań czy też na tej 5 się zatrzymać. Wszystko będzie bowiem uzależnione od skali problemu, jego złożoności, ilości istniejących procesów.
Sam wielokrotnie, podczas prowadzenia analizy zatrzymywałem się na 3 czy 4 pytaniu i było to w zupełności wystarczające. Ale zdarzały się również sytuacje gdzie trzeba było zadać kolejne i kolejne pytanie. Nic nie ogranicza nas by drążyć dalej, szczególnie w chwili gdy nie jesteśmy pewni co do informacji zwrotnej jaką otrzymamy.
Ok. Mamy juz określony problem, mamy zespół analizy problemu z którym doszliśmy do etapu gdzie potencjalne przyczyny zostały nakreślone i czas dokonać bardziej szczegółowej analizy.
Nie zaczynaj od razu od zadawania pytań w celu znalezienia odpowiedzi. W pierwszej kolejności uszeregój potencjalne przyczyny od wagi wpływu na proces. Jeśli będziesz miał ten etap za sobą, zacznij analizować przczyny w 3 kluczowych obszarach;
- dlaczego problem powstał?
- dlaczego problem nie został wykryty?
- dlaczego nie udało się zapobiec powstaniu problemu?
Rozpatrywanie każdej z przyczyn źródłowych z punktu widzenia powyższych obszarów pozwoli Ci znaleźć odpowiedź nie tylko dlaczego problem powstał ale też gdzie są luki w procesach, które pozwoliły na jego powstanie i niewykrycie.
A jak korzystać z 5 Why? Przykład właściwie przeprowadzonej analizy przyczyny źródłowej na poniższej grafice.
Przedstawiony przykład jest prezentuje etapy przejścia od problemu do przyczyny źródłowej.
W naszym przypadku problemem jest to, że samochód nie jedzie. Jak wiadomo, aby samochody o napędzie konwencjonalnym, mogły się poruszać potrzebują prądu do zasilania nie tylko multimediów, świateł czy klimatyzacji ale również a może i przede wszystkim świec zapłonowych (mówimy o silniku benzynowym).
Dla lepszego zrozumienia postępowania z 5 Why? powyższy wykres powinniśmy odczytywać w następujący sposób:
Samochód nie jedzie (Problem) -> Dlaczego? (1) -> Akumulator nie ma prądu -> Dlaczego? (2) -> Alternator nie ładuje -> Dlaczego? (3) -> Pęknięty pasek osprzętu -> Dlaczego? (4) -> Zużyty pasek osprzętu -> Dlaczego? (5) -> Uszkodzone rolki napinacza (Przyczyna źródłowa)
Prawda że proste? Oczywiście można by było drążyć dalej, dlaczego rolki napinacza były uszkodzone itd.
Tę samą zasadę stosuje się gdy chcemy znaleźć przyczyny źródłowe nie wykrywania błędu jak również tego dlaczego nie udało się zapobiec.
Z każdego kroku można oczywiście wyprowadzać kilka pytań dlaczego dożąc do przyczyny źródłowej. Wymaga to jednak bardzo dobrej znajomości zarówno procesu jak i doświadczenia w prowadzeniu analizy przy wykorzystaniy techniki 5 Why? A że praktyka czyni mistrza, to zachęcam do tego by bardziej rozbudowane analizy prowadzić na osobnych wykresach zanim osiągniemy perfekcję w pracy z narzędziem.
Zasady analizy z wykorzystaniem 5 Why?
Jak każda z metodologii, metod czy technik tak i 5 Why? zbudowana jest w oparciu o pewne zasady, które powinniśmy stosować do tego by wykonywane czynności przywiodły nas to oczekiwanego sukcesu.
Poniższe zasady nie są moją własną inwencją twórczą. Wiele źródeł przytacza je jako podstawowe, a wynikają one z założeń, które przyjął sam autor narzędzia.
- Zaangażuj kierownictwo i pracowników do prowadzenia analizy z wykorzystaniem 5 Why?
- Analizę prowadź w zespole. Dla bardziej skomplikowanych problemów zaangażuj tyle osób ile jest Ci niezbędne.
- Pracuj z wykorzystaniem flip-chartów lub tablic a nie komputera.
- Zapisz problem i upewnij się, że wszyscy biorący udział w analizie go rozumieją.
- Oddziel przyczyny od symptomów.
- Zwróć szczególną uwagę na zależności przyczynowo-skutkowe.
- Upewnij się, że zdefiniowane przyczyny źródłowe faktycznie prowadzą do występowania problemu. Możesz dokonać tego poprzez odwrócenie kolejności czytania czyli od przyczyny do problemu.
- Staraj się odpowiadać na pytania precyzyjnie i zwięźle.
- Analizuj przyczynę po przyczynie. Staraj się unikać przeskakiwania pomiędzy różnymi przyczynami nie powodując zamieszania.
- Bazuj na danych, liczbach i faktach.
- Oceniaj proces i system który go buduje a nie ludzi.
- Nigdy ale to przenigdy nie doprowadzaj do sytuacji w której to błąd ludzki jest przyczyną źródłową powstania problemu.
- Zadbaj o przyjazną atmosferę i pewność prowadzonej analizy. Dzięki temu unikniesz konfliktów i przerzucania się winą.
- Zadawaj pytania Dlaczego? do czasu aż uzyskasz pewność, że znalazłeś przyczynę, źródłową.
- W chwili gdy odpowiadasz na pytanie, staraj się patrzeć na proces / produkt oczami klienta (wewnętrznego czy zewnętrznego).
Stosując się do powyższych zasad, z pewnością analiza będzie przebiegała płynniej i będzie prowadziła do właściwych konkluzji.
Celowo jednak podkreśliłem punkt 12. Jest to jeden z najpoważniejszych błędów popełnianych podczas analizy problemu czy poszukiwania przyczyny źródłowej, również przy pomocy 5 Why?. Często by szybko zakończyć analizę uczestnicy skłaniają sie ku konkluzji, że za wszystkimi błędami stoi człowiek.
PAMIĘTAJ! Jeśli człowiek popełnił błąd, to znaczy, że system zarządzania był nieskuteczny, gdyż pozwolił człowiekowi na popełnienie błędu. Przyczyną, która za tym stoi jest najczęściej;
- brak szkoleń
- brak standardów
- niewłaściwie zaprojektowany proces
- brak odpowiednich narzędzi
Te 4 przyczyny są najczęściej głównymi przyczynami źródłowymi stojącymi za błędem popełnionym przez człowieka.
Podsumowanie
Mam nadzieję, że uzbrojony w wiedzę przedstawioną w dzisiejszym wpisie, będziesz w stanie doszukiwać sie przyczyny źródłowej w sposób pozwalający na wyeliminowanie problemów a nie kreowanie nowych czy gonienie za własnym ogonem za ciągle powracającymi problemami.
Jednak, jeśli coś jest dla Ciebie niejasne, chcesz o coś dopytać lub masz uwagi, smiało możesz do mnie napisać. Możesz również wziąć udział w szkoleniach prowadzonych przy udziale Lean Consulting Management Group podczas których metodologia rozwiązywania problemów przy wykorzystaniu m.in. 5 Why? jest dokładnie omawiana.
Zapraszam!